Nut Slot Height
While there’s no substitute for the work of a good luthier, it’s a good idea to understand the basics of guitar setup. That will help you understand how to care for your guitar, what problems you can address at home, and when you need the help of a guitar repairperson.
- Nut Slot Height Strat
- Acoustic Guitar Nut Slot Height
- Bass Nut Slot Height
- Guitar Nut Slot Height
- Proper Nut Slot Height
Excessive Guitar Neck Relief or Forward Bow
3 considerations: Intonation. Action (height) binding or rattle On intonation, generally, if the nut is too high, the extra pressure required will cause the notes on the frets to get progressively sharper toward the nut. I mention this, because on most guitars, the nut slot may be cut slightly back to compensate, so you may leave the nut a little higher than super-low in order to not have to tak. Apologies if this is off-topic. And I'm not disagreeing with anything above; good advice. I never quite got the hang of visualizing nut slot height until someone told me that an open string should have about the same string/fret clearance at the 1st fret that you see when you fret the 1st & look at the string/fret gap at the 2nd fret. For nut slot repair, use the sharp tip to “prime” the bottom of the nut slot by pushing it into the slot at three or four points along it’s width. This helps the new material grip the bottom of the nut slot and resist breaking free prematurely. Put a tiny drop of Krazy Glue in the freshly cleaned slot, careful not to let it run. A slot that is cut correctly should hold the string in place at a height that clears the first fret. Sometimes a guitar nut slot will wear down over time and cause the string to rattle against the first fret, causing the open string to sound a little more like a sitar than a guitar. Guitar technicians measure nut slot depth settings by using a measurement which is equivalent to the distance from the bottom of the string to the top of the first fret wire. This height is measured in thousandths of an inch. It can be a very tiny amount of distance, especially for the high E string.
Is your neck straight?
You can probably recognize excessive curvature in your guitar neck just by looking at it. If you hold the guitar from the body, without touching the neck, and sight down the neck with one eye, you will see if it is straight or not. If the neck has some relief, the middle string height will start low in the open position, be a bit higher along the middle frets and then get low again by the XIIth fret.
What is a truss rod?
The truss rod is often adjusted by inserting a wrench through the soundhole.
When all six strings are tuned to concert pitch, their combined force can easily exceed 100 pounds of tension. This force would naturally bend the neck into a very large forward bow, much like a hunting bow. To prevent this, a metal rod is installed inside of the guitar neck. This is called a . The is not set to a fixed amount of tension, but the tension can be adjusted by tightening a hex key at either the head or base of the neck. It is adjustable because the needed amount of tension may change over time, due to moisture content of the wood or what kind of strings are used.
What is ideal?
The neck should be totally straight, or have a slight amount of forward bow. This forward bow is called , because we relieve the counter-acting tension of the and allow the strings to pull the neck forward—but only a tiny bit.
Don’t be afraid to adjust your truss rod!
The truss rod is not meant to be set once and forgotten, and nor is it considered a job only for experts. Most guitars ship with a truss rod key, and the player is supposed to be able to make adjustments as needed.
If there is too much relief in your guitar neck, the string height along the middle frets V-XII will be very high. You can try to adjust the truss rod yourself. However, if you’ve never done this before, it’s great to try it on a cheap guitar first. If you adjust the truss rod too much, you might cause it to break. You should not adjust the trust rod by more than one or two full turns at a time. If the problem you are experiencing is not fixed after two or more full turns, then you should probably stop and ask an expert, or at least wait a day and try again.
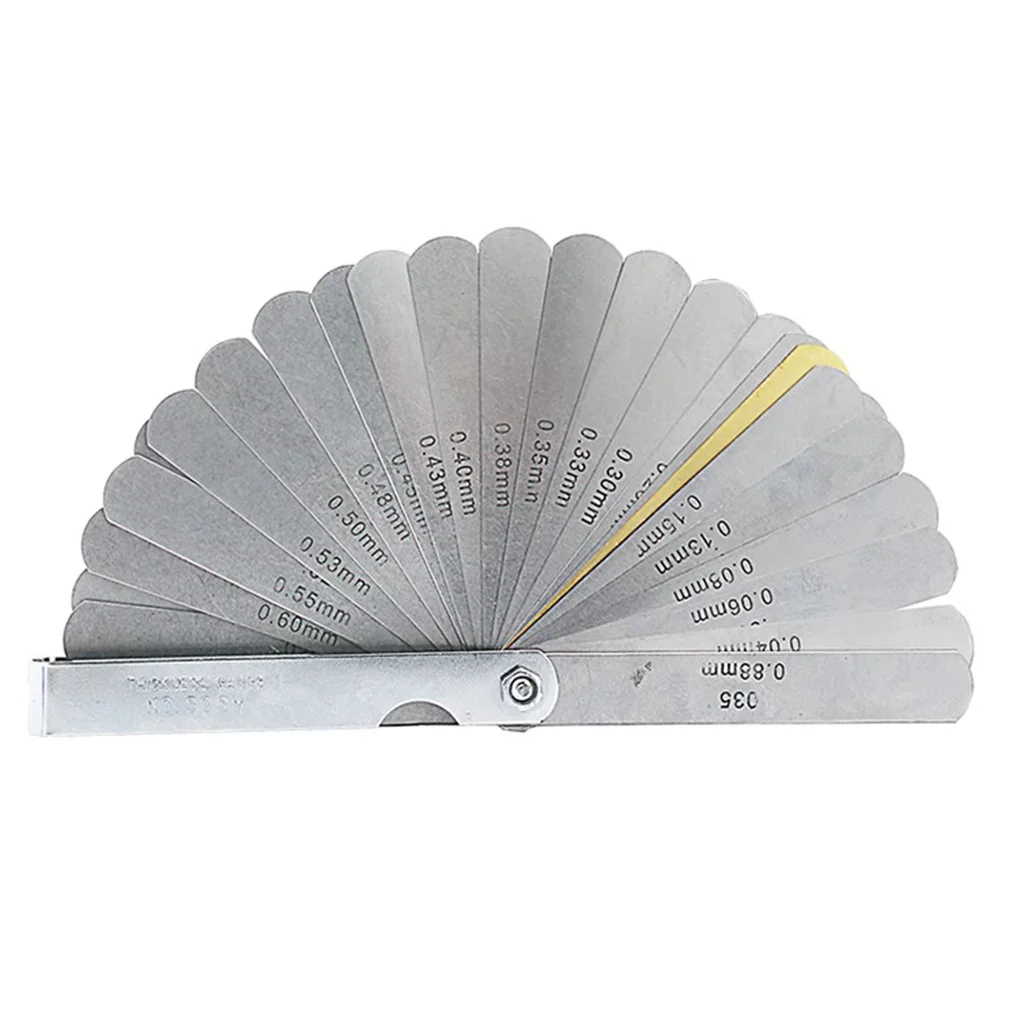
You should also not tighten the truss rod very tight. It should not have the same resistance as the nut on a car tire. It should turn fairly easily. If the resistance is a lot and it is becoming difficult to turn, you should probably stop. Do not add more torque.
It is also best not to make too many sudden adjustments. You can try a quarter or half turn of the trust rod and then stop, wait and observe. You can repeat this process until you’ve found the right setting.
After making your adjustment, sight down the neck again and see if it’s improved.
Because they affect the shape of the wood, truss rod adjustments need a bit of time to sink in. Try doing a quarter or half-turn, and checking again the next day.
Excessive Backbow
Sometimes if a truss rod has been overtightened, or heavy strings are replaced with lighter strings, the neck will begin to have a slight backbow. This is never ideal because the guitar won’t play correctly with a back bow.
The solution is to adjust the truss rod and add a bit more to the neck.
Faulty Nut Slot Height
What’s the ideal nut slot height?
Guitars fresh from the factory rarely get this right. The strings of the guitar rest in slots or grooves that are carved into the nut, which is the small (often white-colored) piece by the guitar’s head, where the strings rest before branching off to the tuning machines.
Because guitars are mass-manufactured, and because getting the correct depth for the nut slot is very difficult and exacting work, most guitars do not ship from the factory with perfect nut slot depth.
What if the nut slot depth is wrong?
If the nut slot is too deep, you will notice immediately because when you play that string open, it will rattle against the first fret. There will be a tinny metallic buzz whenever you play the string open. But if you play any other fretted note on such a string, there is no buzz. This is the tell-tale sign of a nut slot that has been carved too deep.
The string should barely clear over the first fret, with very minimal clearance. Only enough to prevent buzzing. This one is a little bit too high.
If, on the other hand, the nut slot is not deep enough—a much more common situation—it will not be immediately obvious to you. The consequence of this is that the strings are much higher than they need to be over the first fret, which means it will take more force than necessary to depress them in the open position. In other words, because most manufacturers do not ship their guitars with perfect nut slot depth, it may sometimes be difficult to finger open chords on mass-produced guitars.
The irony is that this happens more on “cheap” guitars (less than $1500), so it’s usually beginners who suffer the most from this. And they’re the ones most in need of an easy-to-play guitar!
Measuring the nut slot depth
A guitar that has gotten overly dry may have lower action, and thus have the rattling described above. It is best to first get the instrument fully hydrated before deciding if any setup work needs to be done.

Guitar technicians measure nut slot depth settings by using a measurement which is equivalent to the distance from the bottom of the string to the top of the first fret wire. This height is measured in thousandths of an inch. It can be a very tiny amount of distance, especially for the high E string. The high E string is a mere few thousandths of an inch above the fret wire.
The optimal nut slot depth is as follows: the string should rest as low as possible without producing any rattle or other problems. This would probably be about .010 inches (one hundredth of an inch, or .25mm) of distance between each string and the first fret. Very few guitars are set up to this exacting standard. A measurement of .020 inches or .5mm would be far too high—and yet, this is a common sight on new guitars.
To know for sure, you’ll need to buy an action gauge, such as the Stew Mac Action Ruler This small tool can be found on Amazon for a few dollars and every guitar player should own one! You can also buy a much cheaper one: Baroque Action Ruler.
Adjusting the nut slot depth
If you suspect your nut slots need adjustment, this job is best left to an expert. Of course you can learn how, but it requires patience, some experience, and special tools.
Sharp Frets Protruding From the Side of the Neck
Some particularly cheap instruments are shipped this way. That is, if you grasp the guitar neck with your thumb and index finger, and slide your hand up and down the neck, you will feel the sharp sensation of frets protruding from the side of the guitar neck and scratching your hand ever so slightly. This is far from ideal. You need a smooth surface in order to play the guitar comfortably.
This happens because frets are hammered in roughly and not smoothed out with a fret file. It can also happen due to humidity and temperature changes that cause the wood to contract. The metal fret wire, of course, does not fluctuate as much.
Due to superior construction and wood treatment methods, you won’t often see protruding frets on a high end instrument.
This problem can be fixed relatively easily by filing those frets until they are smooth and no longer protruding.
This is also not much of a do-it-yourself task; you'd have to cover all of the neck’s wood with blue painter’s tape, and use special filing tools to dress the ends.
When shopping for guitars, carefully-dressed frets are one tell-tale sign of good craftsmanship.
Action (String Height) Too High or Too Low
An ideal string height is between .070 and .090 inches above the 12th fret. On this guitar, it’s over .140.
What is action?
The term action describes the height of the strings above the guitar frets. If the action is too high, the strings will be unnecessarily hard to push down to the frets. If the action is too low, then the strings will rattle against one or more of the frets as they are played. Because the strings and the guitar neck do not follow a straight parallel line, this problem is sometimes more apparent on one part of the guitar neck and the other.
Some players prefer a very low action. With a light touch, much of the buzzing can be avoided. To a point. This is especially true for quality instruments. Guitars crafted carefully with excellent fretwork are much more tolerant of low action than inexpensive guitars with hastily installed frets.
If the action of a guitar is too high (which is the most common scenario) then the guitar will play fine, except that it will be harder to push down on the strings. The higher the action, the harder it is to play.
Most new guitars start with action that is too high.
How to Fix a High Action
Lowering the guitar’s action can be done at home fairly easily with a little bit of sandpaper and patience. Be sure the finished saddle sits flat on its bottom edge, unlike this one that was sanded into a slope and now leans to the left.
This is simple enough that a novice can probably address it at home.
You’ll need to take off the strings and remove your . Then, using some medium-grit sandpaper such as 200, sit the saddle on top, facing up as it had been when installed on the guitar, and shave off some of the bottom by pushing down and moving the sandpaper in a back-and-forth motion. Take off a tiny amount: about the width of the line drawn by an ordinary pencil. Now rest the saddle on a flat surface and make sure you haven’t filed a slope into it. If you have, keep working until you’ve got it flat. Reinstall it and string the guitar up. The beautiful thing? If you mess up and sand too low, you can easily shim the saddle back up.
Tip: Using a Stew Mac Action Ruler, measure the string action of the big E string at Fret XII both before and after. This will help you figure out if you’ve made an improvement.
Action (Stright Height) Too Low
Most guitars can’t go much lower than .070' at the 12th fret.
Sometimes an over-zealous action adjustment can result in a string height that is too low.
Especially if it was done in the summer, with high heat and humidity, and now the winter has set in. The lower humidity and heat will cause the wood of the instrument to shrink slightly, and will result in a noticeably lower string height.
Every guitar is different, but most quality guitars can be adjusted to .070' or .080' action at the 12th fret (Big E String). Lower than that and you start to hear alot of buzz. Due to uneven frets and necks that are not perfectly flat and straight, alot of cheaper guitars have to have even higher action.
How to Fix Low Action
This is very easy to fix, and you can do it yourself. Remove the strings, snip up a tiny piece of credit card or similar material to serve as a shim, and stick it under the saddle. Put the saddle back on and voila! higher string action. If it’s still not high enough, do it again—this time with two shims, or—better yet—a thicker shim material.
Since shims are thought by some to affect tone quality, some guitar players even keep two saddles handy: a taller one for winter and a shorter one for summer.
Fret Wear
Over time, frets will wear down. This means that as you fret a note, you might hear some buzz when you play that note because the place where the string contacts the fret has worn itself into a groove. This problem does not affect beginners very often, because it is a direct result of playing a guitar that has been well-worn. Normally beginners start with a new instrument. However, if you bought a used instrument (or inherited one) then you might have this problem as well.
Tall Frets
The exacting work of installing perfect frets is hard to get perfectly right.
If your guitar frets are not of 100% uniform height from Fret I to fret XII and beyond, you may have playability issues.
This is easier for a luthier to address with a simple file and some painter’s tape, but it can be a little time consuming.
Optimal guitar set up
A useful starting point for most guitar learners.
- The neck of the guitar should be as straight as possible, although a small amount of is acceptable.
- The point where the strings rest on the guitar nut and the point where the other end rests on the saddle should form a completely straight line as much as possible.
- The height of the strings from the neck of the guitar should be as low as possible without having any buzzing.
- The depth of the nut slots on the open string should be as low as possible without having any buzzing.
- No fret should be taller than the others, or have a rough, unpolished surface.
- No fret should protrude from the side of the neck in a way that scratches your hand as you play.
- The nut should not have any sharp edges that scratch your hand as you play.
- The strings should be a lighter gauge. 12 is the standard gauge for acoustic guitars, but many beginners will benefit from switching to 11’s or even 10’s. This is less important for electric guitars, for which 10 is a fairly standard gauge.
...with principles that apply, as appropriate, to bridge slots as well
Here's a gnat's-eye view at the face of a nut as seen from the leeward side of the second fret. The slots for these two strings are cut so that they completely support the string.
The sketch above relates to fretted instruments, but the basic principles are no different for violin family and other unfretted instruments. I'll try to explain the clearance in a minute.
Here's an idea of how it works on a bass:
Having the slot cut too high above the frets (or an unfretted board of some type) means that the act of pressing the string down to the first few frets actually stretches the string, raising the pitch and throwing the intonation off in the process. Ideally, the nut slot height is identical to any other fret. But remember that strings can 'saw' themselves through a nut just through normal use. I ordinarily leave a nut slot a little higher than necessary at first, to allow for the string to cut itself a little lower. I also avoid synthetic and elephant ivory, both of which are too soft and rubbery to make good nuts for steel strings.
Nut Slot Height Strat
Here's a shimmed-up mess of a nut that has all the problems:
These slots are all too deep, but the B is still so high it doesn't play in tune, so someone shoved a piece of ebony under it to try and correct the intonation. Big 'Ugh' for this one.
People often comment on certain strings (e.g., mandolin A strings, guitar G strings) being more troublesome, always seeming to go out of tune during play. Mandolin A's are always the most troublesome because they have to make compound bends from the nut: back as well as to one side. And the length from the nut to the post being the other important factor. And being plain strings, they tend to bind if the slots aren't cut right. (The D's, being wound, tend to refine their own slots.)
When you tune, you always tune up to a note, never down, right? Right.
It's about friction in the slot.
And with a poorly cut nut, when you tune up, the tension on the length of string between the nut and the string post is greater (per unit of length) than the part you actually play, that's between the nut and the bridge. After getting the pitch just right, a bit of actual playing works the string, making the tension on both sides of the nut equalize, and voilà: you're out of tune in mid-phrase. It has nothing to do with the tuning machines, which people just love to blame, but everything to do with setup, particularly how precisely the string slots at the nut are cut.
A quick word about creaking guitar G strings: this issue is fading as elephant ivory nuts are fading. Bone is superior to ivory for a nut material because it's harder and burnishes better. Ivory is soft and actually registers the imprint of string windings. That irritating creak is the sound of the windings skidding over grooves impressed inside the nut slot. Once again: setup is everything. (You can resurface string slots in an ivory nut by inlaying bits of with pearl or bone, if you like.)
How do you easily determine the ideal height of the string slot in the nut? OK, start with ⓵:
Acoustic Guitar Nut Slot Height
The string is a superb straightedge when it's under tension. This assumes the frets are really true and level.
The sketch below illustrates how - and how not - to shape a slot for any string.
Left: like the messy nut above, the nut material is too high. You need only enough to support half the diameter of the string. Anything more is just in the way. When the string is way below the top of the nut, you have great difficulty telling whether it's seating properly.
Next: a slot that's cut with a saw has a roughly flat bottom and also affords poor acoustic coupling. Saws seldom match the precise width of the string, which can roll side to side in the slot.
Next: strings will work their way down a v-cut, often bottoming out on frets (or the board, as the case may be with fretless instruments). The signal transfer is compromised because of the limited contact, and the string sizzles on the fret or the board. They also tend to bind and squeak. They can ruin your day.
Right: the slot really fits the diameter of the string, the nut material does not go above the halfway point of that diameter, and leaves the string a trace of clearance above the fret or the unfretted board surface.
How much is a trace? I'm reluctant to assign a measurement—it's very little. You can still see a bit of light.
If you hold any string down on any fret of a well set up instrument, you'll see that same preferred clearance at the next fret up.
Before going further, here's how to correct a string slot that's too low. Often it's wiser to repair a blown slot than it is to replace the whole nut.
Quick fixes like some kind of dust (bone, acrylic, baking soda) with superglue are really temporary. It takes little more effort to implant a little patch of bone (or even pearl) into the nut and recut the slot. It's as good as the original, and if done well, is quite invisible.
Bass Nut Slot Height
I have a couple of saws I use for widening and deepening in preparation for an implant. One is a fine hacksaw blade in a short handle, which is for wider strings. It leaves a nice flat-bottomed slot. The other is a backsaw such as one would use for cutting fret slots, which does the same and is good for finer strings. Avoiding hitting the first fret, assuming there is one, I cut down below the blown slot, sometimes almost to the board itself, angling the saw back a bit. Then I prepare the piece of bone (or whatever: ebony for a violin or cello) by carefully filing a piece of the material with a fine flat file until it slips snugly into the slot. I usually use old saddle scraps for this. A drop of CA and a tap and it's in there:
Trim and dress the nut as if it was new and uncut, then cut the new slot.
The slot itself needs to be shaped in a way that it not only fits the diameter of each individual string, but also such that the string has firm contact with the nut at the very front of the slot. This defines the end of the vibrating string length, and if it's not right, intonation will be impaired at the very least, and you may well find your string sizzling like a sitar string.
I prefer to shape my slots in the shape of a horn's bell:
The point of this is to offer a smooth surface for the string to travel from the tuning machine to the critical point of final contact at the front of the slot, where it is held firmly to define the end of the vibrating string length.
Strings have to make a compound bend at the nut, and to make tuning easiest while ensuring complete firm contact at the front of the slot, this horn bell shape makes certain the string glides smoothly, no matter the angle of approach. Here's a treble side view:
The bell here is imaginary. The nut is in yellow, the fingerboard is dark brown. The string is the green line, and the tuning machines are off to the right somewhere. Notice that the string connects with a smooth curved surface, no corner or edge. Whether the string is coming from the top or the bottom of the string post, it will slide smoothly into the nut slot. The string is in complete contact with the front 30% of the nut. There's plenty of substance there to keep the string from sawing its way deeper into the bone.
Here's the same slot seen looking straight down from above:
The string's other curve, from, say, the farthest peg on the bass side of the headstock, also elides with the inside of the bell-shaped slot, guided gently and directly to the front where it's held firmly by its own tension inside the confines of a well cut slot.
If the slot isn't properly angled back, several problems can arise.
If it's too flat (some repair books actually advocate this!) the string soon wears away the front of the slot and the functional point of contact is as much a 40% of the width of the nut back from the front edge, which can cause the note to ring poorly (because it's vibrating along a surface, not held to a point) and perhaps cause intonation problems. This is bad:
If the slot is angled back, but left a straight line, it will bind on the back edge, and the front edge will wear down from playing and the string is at risk for sizzling on the first fret or on the surface of the board. This is also bad:
The precise shape of the slot at the front edge is extremely important for sound quality, stability of the setup, and intonation.
Guitar Nut Slot Height
More on bridges in due time, but the principles here apply to bridge slots on the viol and violin families, guitars, mandolins, and so on.
Here's a page on the files and so on you need to cut nuts.
Proper Nut Slot Height
Back to the repair index page.